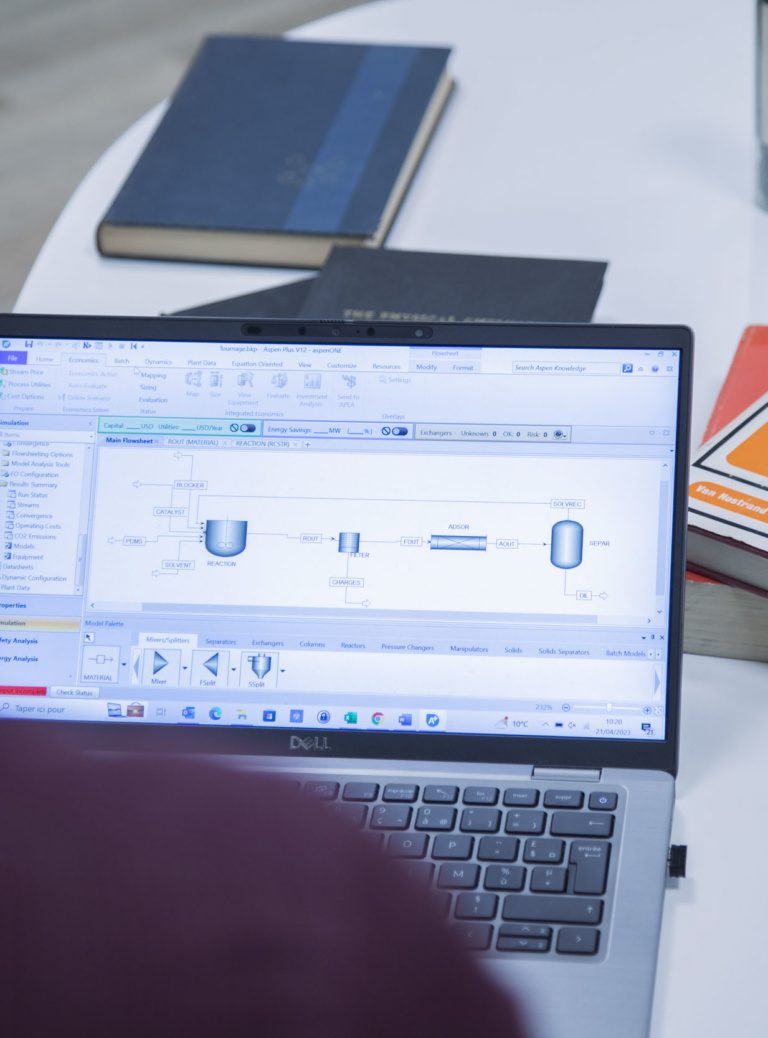
01. The 4 stages of process development
Process development requires the application of a rigorous, adaptable methodology to optimize performance while minimizing environmental impact and controlling the risks associated with industrialization. This methodology must make it possible to integrate technical and economic performance, sustainability and safety assessments right from the early stages of development, while ensuring a rapid and controlled transition to industrial scale. By structuring the design, sizing and validation stages, it helps to reduce time-to-market, a key competitive factor in a constantly evolving industrial context.
1. Acquisition of basic data and characterization of process conditions: the first step in process development is to collect and analyze the physical properties of the products, as well as thermodynamic data (reaction enthalpies, heat transfer coefficients, phase equilibrium, etc.) and kinetic data (reaction rates, reaction orders, influence of operating parameters, etc.). Rigorous characterization forms the basis for selecting the most suitable technologies, defining the sequence of unit operations (reaction, separation, purification) and, finally, optimizing overall process performance while anticipating the risks associated with scale-up.
2. Comparative studies and process selection: the second phase of process development consists in identifying the most appropriate production solution. For this purpose, digital technology selection tools (such as PROCIP), as well as process modeling and simulation software such as Aspen Plus, are used. Thanks to the experience of specialized engineers, and backed up by previously acquired data, these tools will enable us to predict the performance of the various processes envisaged. Added to this, techno-economic studies and life-cycle analyses (LCA) will enable the most efficient, reliable and sustainable process to be selected.
3. Laboratory and pilot scale: first on a small scale, then on an intermediate scale, also known as ‘pilot scale’, this stage consists of experimentally testing the process under development. This phase is essential for validating numerical models and simulations under conditions close to those of industrial production. It is also particularly useful for adjusting operating parameters and ensuring that the process meets safety, sustainability and profitability criteria. It also plays a key role in the production of representative samples, enabling us to validate product application properties and their suitability for market requirements. Finally, by securing the scale-up, this progressive stage will play a central role in the sizing and manufacture of the final equipment, thus derisking the industrial investment.
4. Industrialization: the final stage of process development marks the crucial transition from the laboratory to large-scale production. It includes the consolidation of the process book, which gathers all the data required for engineering studies, right up to the construction of the industrial or demonstration unit. Good communication and effective handover between the development and industrialization teams are essential to the success of the project.
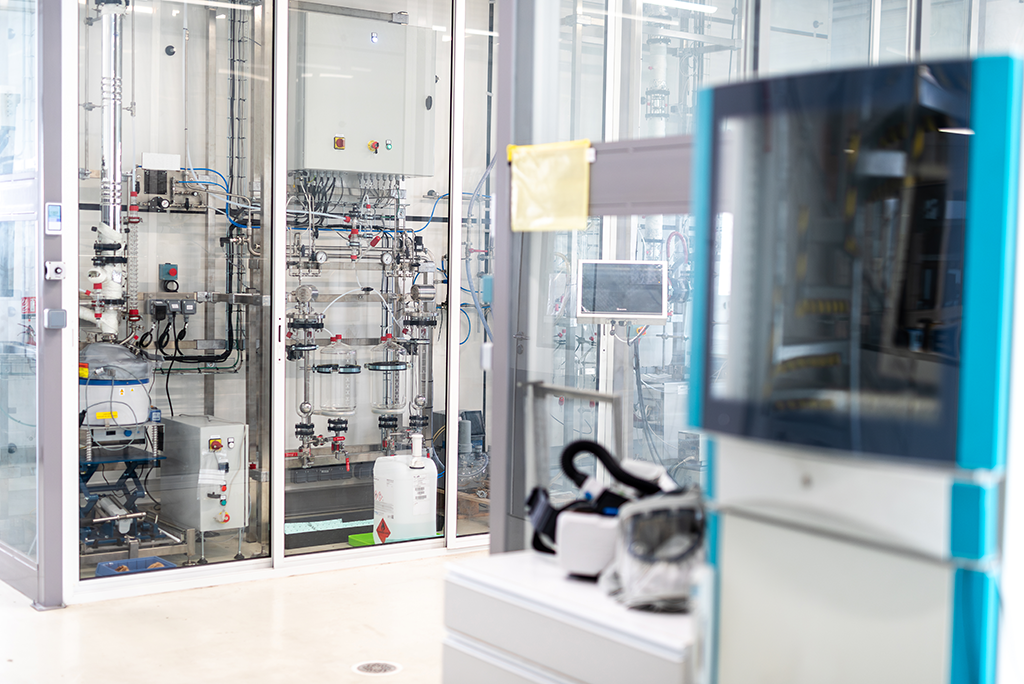
Pilot hall
02. The process development at the center of the ecological transition
Process development plays a key role in the evolution of many industrial sectors, responding to the specific needs of each field while meeting today’s environmental and economic challenges.
➡️ The chemical industry and the circular economy
Historically, the development of chemical processes has led to spectacular advances. For example, the Haber-Bosch process, designed in the early 20th century, made possible the large-scale production of ammonia, essential for agricultural fertilizers. This innovative chemical process fundamentally transformed global agriculture, making it possible to feed billions of people.
Today, the chemical industry must reinvent itself to meet the challenges of the environment. The need for energy sobriety and the need to reduce effluents have prompted all players in the industry to move towards more sustainable practices. Numerous initiatives to make sustainability rhyme with competitiveness have emerged, such as the development of new methods for recovering plastic materials (read our article about REPOS project). These new processes promote a circular economy, thanks in particular to the reuse of silicone waste. To bring these large-scale projects to fruition, the need for process design and development is considerable.
➡️ Biobased products as an alternative
Biobased processes play a key role in the transition to a more sustainable industry, exploiting renewable natural resources to design innovative products or offer more environmentally-friendly alternatives to existing products. In particular, they rely on the use of renewable carbon, derived from biomass, to replace fossil raw materials traditionally used in chemistry and materials.
An emblematic example is the conversion of agricultural biomass into biodegradable bioplastics, a promising alternative to petrochemical-based plastics. Thanks to advances in biotechnology, the development of innovative processes such as microbial fermentation is now making it possible to produce biobased polymers such as polyhydroxyalkanoates (PHA), 100% compostable bioplastics with properties comparable to those of conventional plastics. A rigorous approach to the development of biosourced processes ensures their economic and environmental viability by controlling the associated impacts.
➡️ Decarbonization
Industrial decarbonization is a major challenge for reducing the carbon footprint of production processes and limiting greenhouse gas emissions, particularly carbon dioxide (CO₂). In this context, the development of innovative technologies enabling the capture and recovery of CO₂ represents a strategic step forward towards a more environmentally friendly industry.
The VIVALDI projet is fully in line with this dynamic, exploiting CO₂ emissions from biorefineries to transform them into organic acids, such as acetic acid, through a microbial fermentation step. Rather than being released into the atmosphere, this CO₂ is thus used as a raw material for the production of high-value-added molecules, reducing dependence on the fossil resources traditionally used for their synthesis. By integrating Carbon Capture and Utilization (CCU) strategies, the VIVALDI project illustrates how technological innovation can not only limit the climate impact of industries, but also develop new low-carbon production channels.
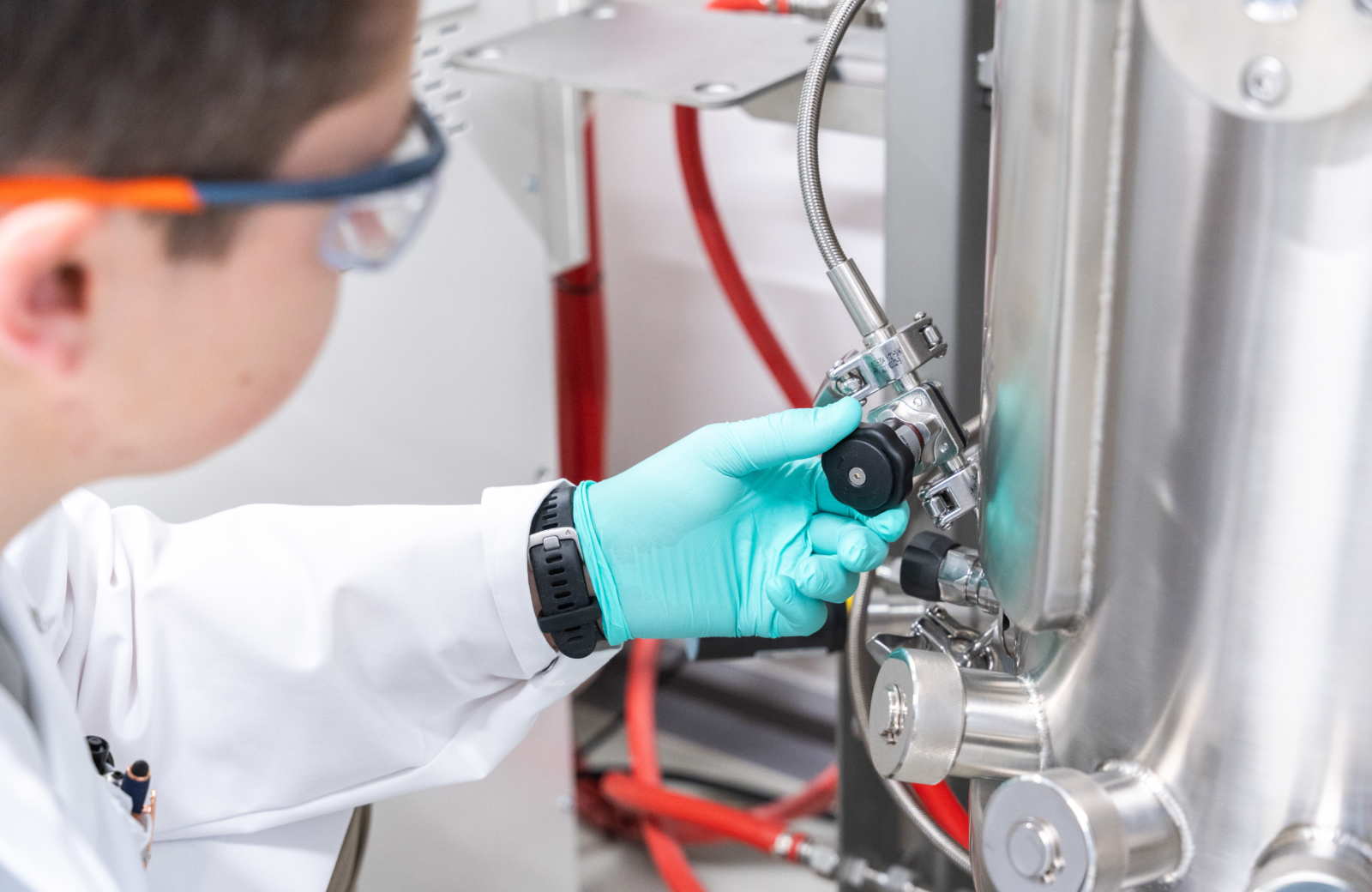
03. Conclusion
Process development is a strategic pillar of industrial transformation, combining science and engineering to optimize the conversion of raw materials into high value-added products. It is a complex process that follows several key stages, each essential to guarantee the efficiency, safety and sustainability of the final process. Throughout this development, it is essential to follow a rigorous methodology, integrating both advanced technological tools and human expertise to anticipate challenges and minimize risks. Thanks to its recognized experience in the process field, Processium has made a name for itself as a leader in the development and industrialization of innovative processes. Its know-how guarantees tailor-made support, ensuring customized solutions that meet the specific requirements of each project.
Finally, today, more than ever, process development offers concrete solutions for meeting environmental challenges, reducing CO₂ emissions, and improving the sustainability of industrial activities. By integrating innovative technologies such as CO₂ emissions recovery or the production of biosourced bioplastics, industrial processes are becoming key players in decarbonization and the energy transition. This development, focused on circular and low-carbon approaches, represents a major lever for an industrial future that is both competitive, responsible and respectful of global environmental issues, by placing resource optimization and the reduction of ecological footprints at the heart of industrial strategies.